If you’re in manufacturing or construction, you’re no stranger to the flood of engineering diagrams that cross your desk daily. But did you know some symbols you’re casually deciphering have origins dating back centuries? That’s right—you’ve been staring at a piece of engineering history without even realizing it!
If you dig a little deeper into history, you’ll find that some engineering symbols date back even further and have interesting backstories. Engineers didn’t just use these symbols to build things—they sometimes tweaked them to include secret messages in blueprints - a common practice during World War 2. Sensitive projects were often disguised under code names, and slightly altered symbols were a clever way to keep things in secrecy.
The engineering drawings started getting standardized in the early 20th century, giving us the familiar set of symbols we currently rely upon. Today, engineering drawing symbols serve as a universal language for engineers, constructors, manufacturers, and contractors, providing clear communication across technical documents. The contemporary set of engineering drawing symbols covers various disciplines, including electrical, mechanical, civil, and architectural engineering.
Key categories include:
Line Types: Indicate the type of feature, such as solid lines for visible edges, dashed lines for hidden edges, and centre lines for symmetry.
Geometric Tolerances: Symbols that define allowable variations in a part's geometry, ensuring precision in manufacturing.
Welding Symbols: Provide details on the type, size, and location of welds.
Electrical Symbols: Represent components like resistors, capacitors, and switches in circuit diagrams.
Flowchart Symbols: Used in process and instrumentation diagrams (P&IDs) to depict the flow of materials and control systems.
These symbols are standardized internationally through organizations like ISO and ANSI, ensuring consistency and clarity across all engineering documents.
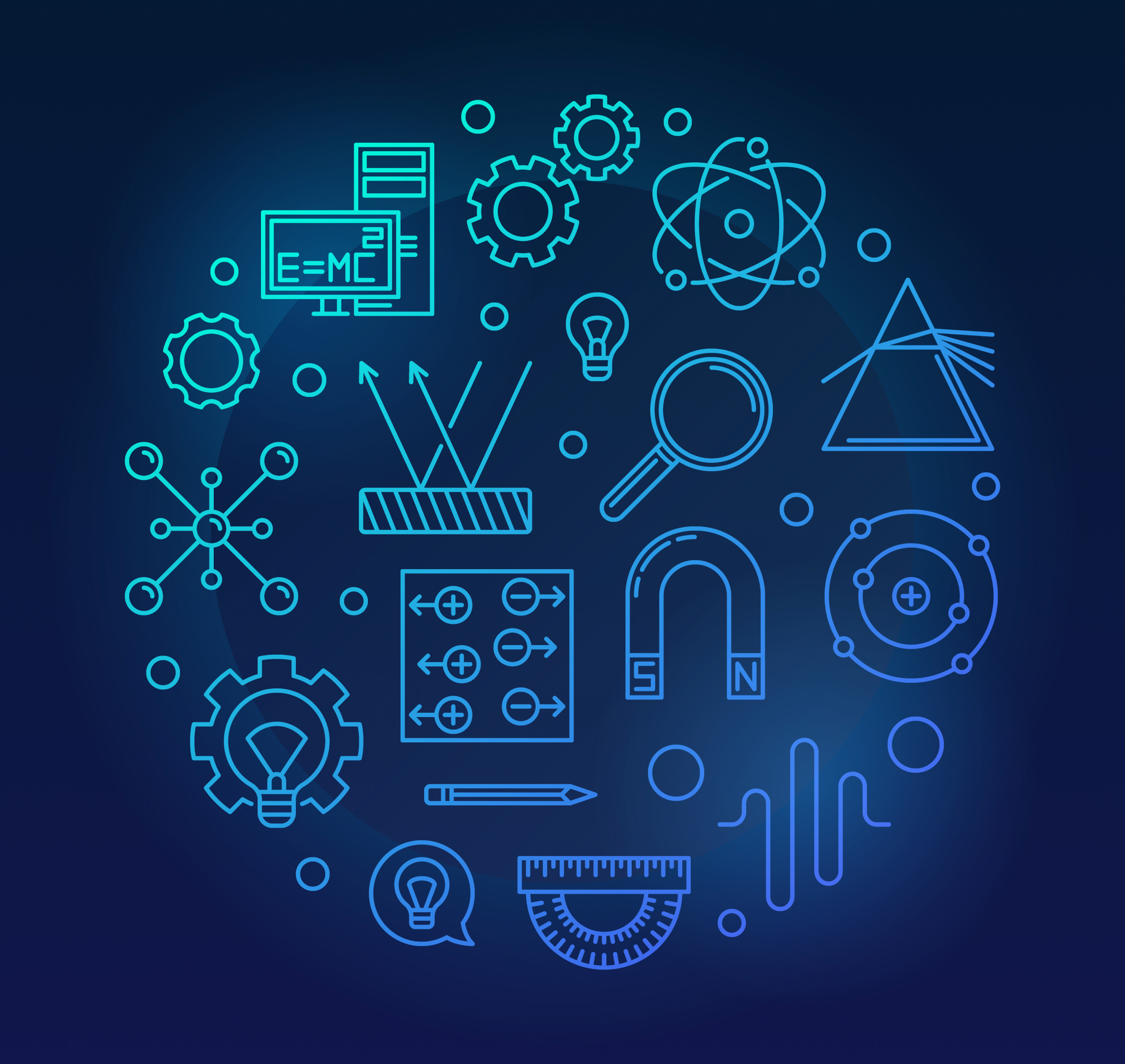
However, the usage of code names and unique symbols for sensitive projects is still very much alive. In today’s high-tech and defense industries, this practice has evolved well, keeping pace with advancements in technology and security. Even now, specialized symbols and code names are the go-to for obscuring the details of confidential projects and safeguarding intellectual property. But that’s not all - certain firms and offices have their unique symbols, adding a delightful layer of diversity to the mix, despite the push for standardization.
What adds up to the complexity of interpreting these symbols is the ever-changing regulatory landscape of engineering drawings. New symbols are constantly being added to standard sets to keep up with the relentless march of technology and innovation. And in the last decade, there’s been a noticeable surge in symbols related to automation and smart technologies, mirroring the sector’s leap into Industry 4.0.[1] So, while we may have a solid foundation of standardized symbols, the field is anything but static—it’s a living, breathing entity that’s continuously evolving.
“The International Organization for Standardization (ISO) and the American National Standards Institute (ANSI) typically update their regulations every five years.” [2]
Keeping up with the latest symbols and conventions in engineering drawings is no easy task, especially when relying on manual interpretation. The risk of errors, misinterpretations, and inefficiencies skyrockets as new symbols are introduced, and traditional tools often struggle to keep pace.
This is where automated tools and intelligent systems come in—image detection technology can revolutionize the reading of engineering drawing symbols by automating the interpretation and extraction of data from complex diagrams. Unlike manual methods and traditional tools for engineering drawings that are slow and prone to errors, contemporary image detection technology relies on advanced algorithms that can quickly identify and classify symbols, lines, and annotations within engineering drawings.
They can rapidly adapt to changing regulations, ensuring that complex and constantly evolving engineering drawings are interpreted with accuracy, consistency, and speed. Hole detection, extension analysis, and screw placements are seamlessly processed. Plan evaluation, machining precision, and figure recognition become more efficient. Threads, surface quality, and pitch measurements are accurately extracted. Software-driven solutions enhance material assessments, training modules, and finish quality checks.
Let’s Crack the Symbol
In manufacturing and construction, thousands of engineering diagrams circulate within companies, packed with crucial information for teams in R&D, production, quality assurance, design, and maintenance. The secret to efficiency in each of these processes lies in how quickly and accurately this information can be extracted, which in turn relies on the automation of data extraction. Let's face it: with so many tools available, choosing the right one can be challenging. But don’t worry—we’ll break it all down in this blog. So, keep reading!
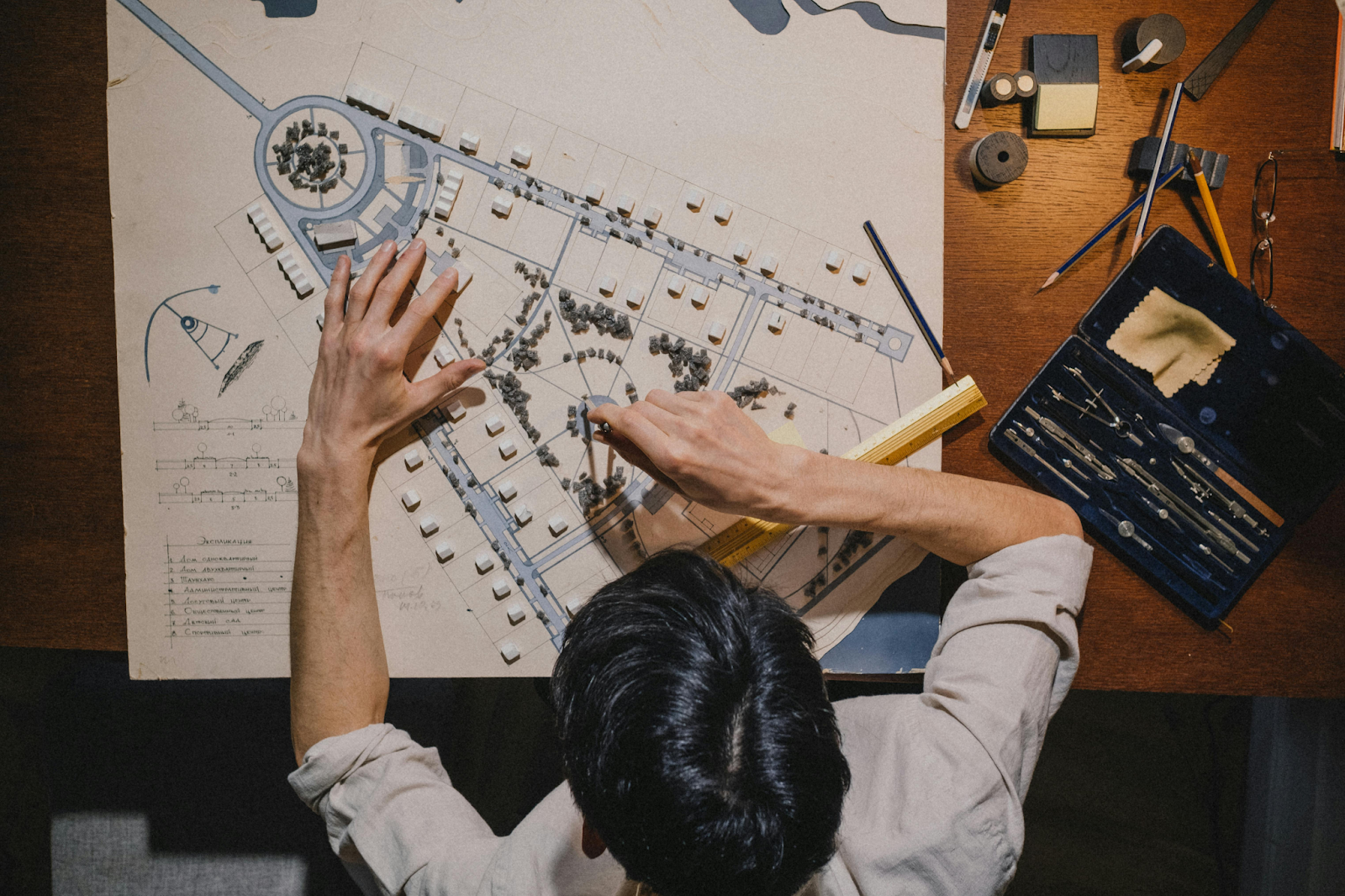
“Engineering diagrams are not just drawings; they are the roadmap from imagination to reality.”
Unlike engineering models that just show you the big picture, engineering drawings dive into the details, covering everything from dimensions to materials. They’re the blueprints that guide engineers through the complex steps of making and assembling something great.
What are Engineering Drawing Symbols, and Why Do They Matter?
Engineering drawing symbols are standardized icons representing dimensions, materials, and processes in technical drawings. They serve as a universal language, enabling engineers, architects, and manufacturers to convey complex information with precision and clarity, ensuring effective communication across disciplines and transcending language barriers.
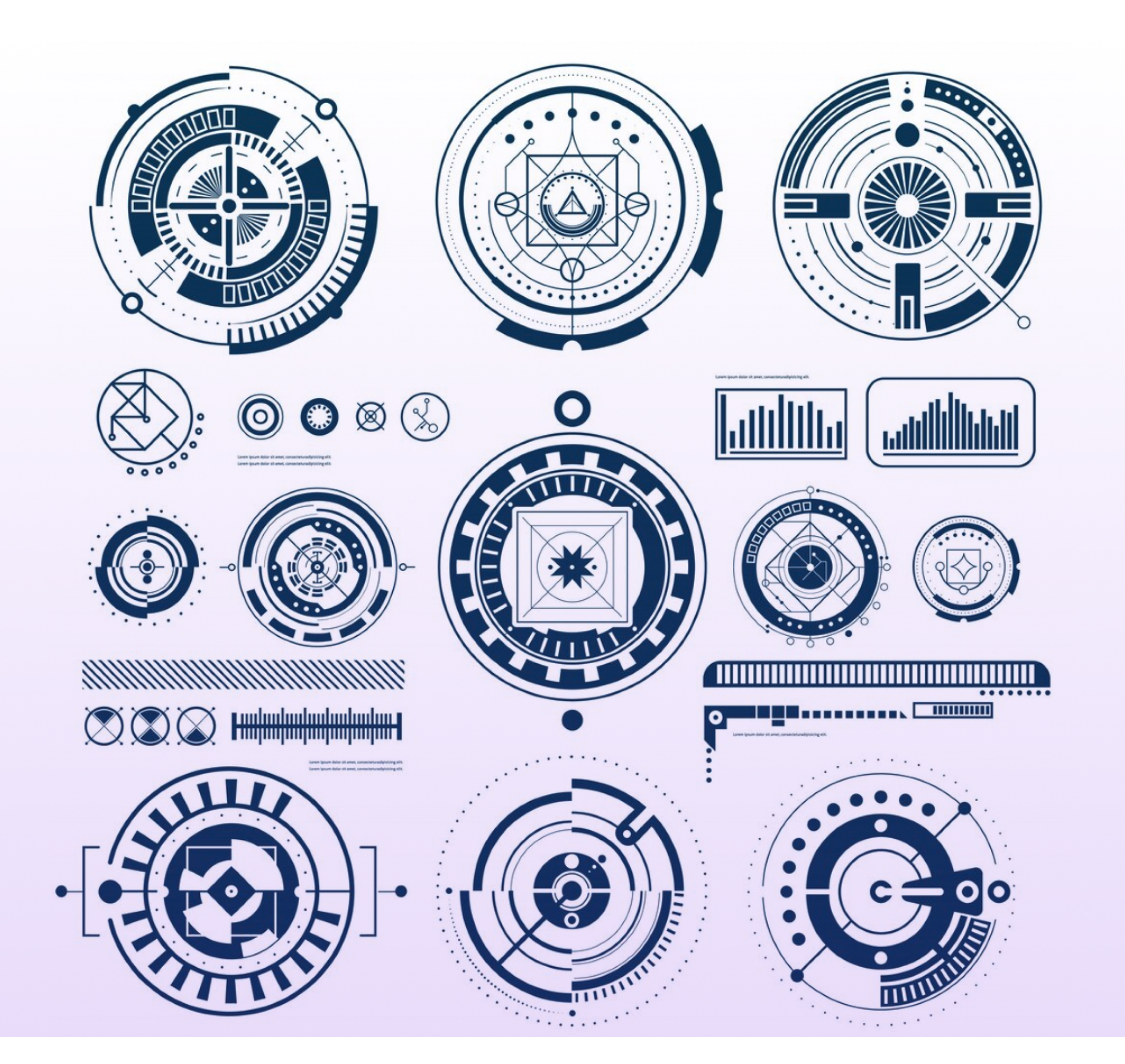
Types of Engineering Drawing Symbols
There is a standard set of engineering drawing symbols that are widely used across industries to ensure consistency and clarity in engineering diagrams. These symbols are defined by various international and national standards, such as:
- ISO (International Organization for Standardization): The ISO 128 series, for example, covers general principles of presentation, including symbols used in technical drawings
- ASME (American Society of Mechanical Engineers): ASME Y14.5 is a well-known standard in the U.S. that defines symbols for geometric dimensioning and tolerancing (GD&T)
- IEC (International Electrotechnical Commission): IEC 60617 provides a comprehensive collection of graphical symbols for electrical and electronics engineering
- ANSI (American National Standards Institute): ANSI Y32 and ANSI Y14.36M provide standards for fluid power, piping, and electrical diagrams.
Common Challenges in Reading Engineering Drawings, Interpreting Symbols
Navigating engineering drawing is like solving a complex puzzle where the pieces are constantly shifting. Here are some common hurdles that may slow you down while reading them.
Complexity and Ambiguity
The challenge begins with the inherent complexity of the symbols themselves. Many symbols are intricate and can appear similar, yet their meanings vary based on context, rotation, or scale. This potential for ambiguity can easily lead to misinterpretations, especially when symbols are manually read. A single misread line or incorrect assumption about a symbol’s function can cascade into significant errors, disrupting workflows and escalating costs.
The challenge intensifies when trying to maintain consistency across different diagrams. Ensuring that symbols are used correctly and uniformly throughout various documents can be daunting, as even minor inconsistencies may result in significant complications in design, construction, and manufacturing.
“ Errors and inaccurate construction can result in high-cost rework and weeks or months of project delays. 5-12 % of material and labor budgets are often lost to rework, schedule delays, and downstream communication clashes.”[3]
Manual Errors
Manual interpretation of engineering drawings is fraught with the potential for errors and misinterpretations. Human readers may misread complex symbols or overlook subtle details, leading to incorrect assumptions or omissions. Variations in individual expertise, fatigue, and inconsistent practices can further exacerbate these issues. A single error in understanding a symbol or dimension can ripple through the entire design or manufacturing process, resulting in costly mistakes and delays.
“When thousands of individuals and numerous companies work together on multimillion-dollar projects with countless components, achieving perfection requires rigorous data checks, verification, and quality control.”
Calculation Errors
Calculation errors in reading engineering diagrams occur when incorrect interpretations or miscalculations are made based on the symbols and measurements depicted. These errors aren’t mere theory-based assumptions. They cause significant financial losses to businesses every year.
Time to Move On From the Traditional Tools & Feature(s)
Traditional image recognition approaches face significant limitations in engineering drawing reading. These methods often rely on pattern recognition alone, failing to account for the crucial context needed to interpret symbols accurately. For example, the same letter or digit can have different meanings based on its location, and lines that appear identical to a computer vision model can have vastly different interpretations.
As a result, the task remains only partially automated. While various tools help engineers convert scanned drawings into digital models, current software solutions only address a small portion of the process. Most of the work is still labor-intensive and time-consuming, making digitizing engineering drawings a challenging and inefficient task.
All Thanks to Tech
Fortunately, technological advancements are making these challenges more manageable. Modern symbol recognition techniques, driven by neural networks and extensive datasets, have significantly improved. These systems can accurately locate and classify symbols even with variations in rotation, scale, or font. Using scale-invariant raster representations, they handle the complexities of symbol recognition effectively, reducing human error and enhancing accuracy. By leveraging these advancements in computer vision, we can interpret engineering drawings with greater precision and efficiency.
Entering the World of Automation with Image Detection for ED
Manufacturers, contractors, subcontractors, field engineers, and project managers should consider the idea of automating the most cumbersome and crucial process - ED drawings data extraction automation. The quick and precise interpretation of these diagrams is crucial for better tolerance detection:
- Streamlined Production: Engineering drawings provide detailed instructions on dimensions, materials, and assembly processes. Automating their reading ensures that these details are processed swiftly and accurately, reducing the time required for manual interpretation and minimizing the risk of errors that could disrupt production schedules.
- Cost Efficiency: Errors in interpreting engineering diagrams can lead to costly rework, delays, and waste. By automating this process, companies can significantly reduce the likelihood of mistakes, ensuring that materials are used effectively and production steps are executed correctly the first time. This translates into lower operational costs and increased profitability.
- Enhanced Consistency: Automation ensures that every drawing is read and interpreted uniformly, regardless of who is operating the system. This consistency helps maintain high-quality standards across all products and projects, avoiding discrepancies arising from varying human interpretations.
- Faster Turnaround Times: In a competitive manufacturing environment, speed is critical. Automated systems can process engineering drawings rapidly, enabling faster decision-making and quicker turnaround times for product development and manufacturing. This agility can be a significant advantage in meeting tight deadlines and responding to market demands.
- Improved Data Management: Automated reading systems can integrate with other digital tools and databases, providing real-time updates and facilitating better data management. This integration supports more effective tracking, reporting, and analysis of engineering data, enhancing overall operational efficiency.
How it Started
Although the theoretical foundations for automatic engineering drawing reading were established by the late 1990s after over 25 years of academic research, it is only in the past five years that technological advancements have made practical industrial implementation possible. This recent progress represents a breakthrough, transforming long-standing theories into actionable solutions in the field.
The first technology developed for the automated reading of engineering diagrams was Optical Character Recognition (OCR). Early OCR systems, introduced in the 1950s and 1960s, were initially designed to read printed text but later adapted to interpret and process various types of diagrams and engineering drawings. However, OCR does not fully meet the intended purpose due to its inefficiency in interpreting complex or non-standard layouts, such as intricate engineering diagrams with varied symbols and formats.
Engineering Drawing Scanners play a crucial role in digitizing physical drawings, allowing for easy storage, access, and manipulation of complex engineering diagrams. Introduced in the late 20th century, these scanners convert intricate paper-based designs into digital formats that can be integrated with Computer-Aided Design (CAD) systems. Despite their advantages, scanners face drawbacks such as difficulty in accurately capturing fine details, distortion of scanned images, and challenges in interpreting complex symbols and layouts, which can limit their effectiveness in processing highly detailed or non-standard engineering drawings.
How Its Going: The Emerging Trends in Engineering Drawings
As technology continues to evolve, so do the methods for reading and interpreting engineering drawings and symbols. From advanced machine learning algorithms to innovative automation tools, the following tech innovations are reshaping the landscape of engineering documentation and offering new solutions to long-standing challenges.
- AI and Machine Learning
- Integrated CAD Software
- Enhanced 3D&5D Modeling
- Augmented Reality (AR) and Virtual Reality (VR)
- The eDOCr Tool
- RPA
- Integrated Design Tools
Reading Engineering Drawings with Advanced IDP
Advanced Intelligent Document Processing (IDP) enhances the reading of engineering diagrams by integrating AI, machine learning, and contextual analysis. IDP offers a more sophisticated approach, unlike traditional Robotic Process Automation (RPA) and Optical Character Recognition (OCR), which may struggle with complex symbols and contexts
Advantages of AI-Native IDP over RPA and OCR:
- Contextual Understanding: IDP systems analyze the relationships between symbols and their positions in the diagram, providing a more accurate interpretation of complex engineering drawings.
- Enhanced Accuracy: By leveraging AI and machine learning, IDP improves the recognition of varied and intricate symbols, reducing errors that can occur with standard OCR or RPA.
- Adaptability: IDP can adapt to different formats and symbols over time, learning from new data and improving its performance, whereas traditional OCR and RPA tools may require manual adjustments.
Dealing with complex engineering diagrams can often get challenging. But remember, errors are a part of the process, but catching and addressing them early is what truly matters. Fortunately, with automation technologies like Gen-AI-led IDP for symbol detection, scanning, and calculations, you can now manage these complexities with greater ease. Embracing these advanced technologies can help simplify your tasks and improve accuracy. These innovations are designed to support you and make the process smoother so you can focus on what you do best!
References
1) How Engineering Fits into Industry 4.0." RS, May 14, 2024. Last modified May 14, 2024.
2) International Organization for Standardization. ISO 129-1:2018: Technical Product Documentation (TPD) — Presentation of Dimensions and Tolerances. Geneva: International Organization for Standardization, 2018.
3) AEC Industry Report: OH, CRAP! 10 of the Worst Construction Blunders and How You Can Avoid Them. April 2018. Sponsored by ClearEdge3D. Contributors: Kelly Cone, Buck Davis, Anton Dy Buncio, Will Ikerd, David Thirlwell.
Resources
Musa, Shamsudeen. "Effects of Design Errors on Construction Projects." International Journal of Scientific and Engineering Research 7, no. 2 (February 2016): 1099-1114. University of Malaya.
FAQs
Using AI for pre-fund QC audits offers the advantage of quickly verifying that loans meet all regulatory and internal guidelines without any errors. AI enhances accuracy, reduces the risk of errors or fraud, reduces the audit time by half, and streamlines the review process, ensuring compliance before disbursing funds.
Choose software that offers advanced automation technology for efficient audits, strong compliance features, customizable audit trails, and real-time reporting. Ensure it integrates well with your existing systems and offers scalability, reliable customer support, and positive user reviews.
Audit Quality Control (QC) is crucial for mortgage companies to ensure regulatory compliance, reduce risks, and maintain investor confidence. It helps identify and correct errors, fraud, or discrepancies, preventing legal issues and defaults. QC also boosts operational efficiency by uncovering inefficiencies and enhancing overall loan quality.
Mortgage review/audit QC software is a collective term for tools designed to automate and streamline the process of evaluating loans. It helps financial institutions assess the quality, compliance, and risk of loans by analyzing loan data, documents, and borrower information. This software ensures that loans meet regulatory standards, reduces the risk of errors, and speeds up the review process, making it more efficient and accurate.
Yes, AI can identify and extract changes in revised engineering drawings, tracking modifications to ensure accurate updates across all documentation.
Yes, advanced AI tools can recognize and extract handwritten annotations from engineering drawings, capturing important notes and revisions for further processing.